Serialization and Its Role in Managing Drug Recalls and Returns
Serialization forms a core component of the global pharmaceutical manufacturing process, ensuring the traceability, authenticity, and safety of pharmaceutical products throughout the supply chain.

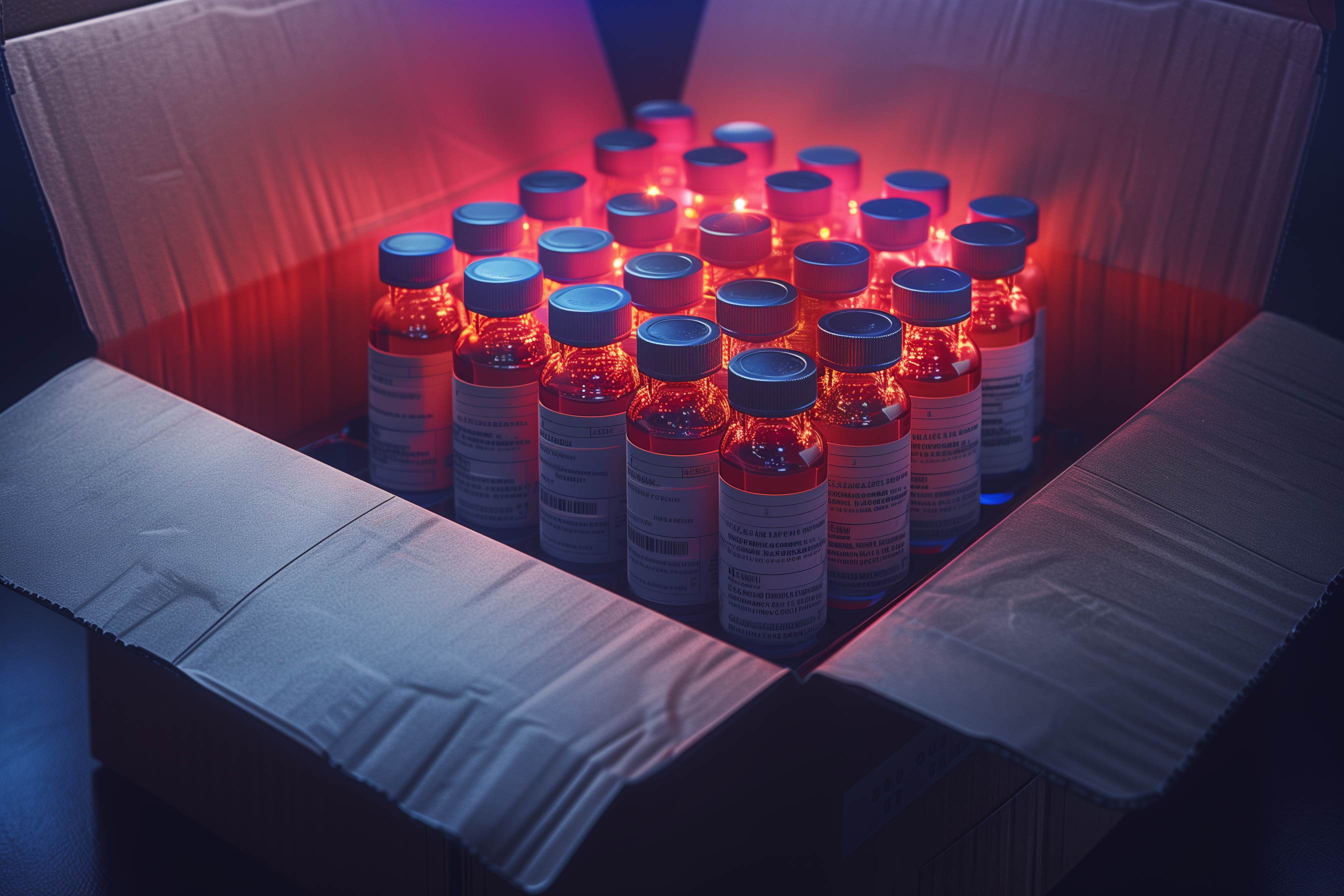
Much has been written about serialization’s role when it comes to adhering to global regulatory standards, and as a way of fighting counterfeit medication.
However, another core function is to drive the recall and returns process of drugs – a task that usually needs carrying out urgently if such a situation arises. Let us examine just how important serialization is for the global drug recall process – and analyze its future trends.
What is Serialization?
Pharmaceutical serialization refers to the process of assigning a unique identifier, typically a serial number, to each individual package of a pharmaceutical product.
This identifier is typically encoded in a 2D matrix, barcode or a similar machine-readable format and is used to track and trace the product throughout the supply chain, from manufacturing to distribution and ultimately to the patient.
Each product is assigned a unique identifier during manufacturing which is printed on the product packaging as a barcode or other unique physical marking. The serialization data is then uploaded to a secure database, often managed by manufacturers or third-party providers. At each stage of the supply chain, the product’s barcode is scanned and verified, ensuring authenticity and traceability.
Many countries now mandate serialization to comply with drug safety regulations, such as the U.S. Drug Supply Chain Security Act (DSCSA) and the European Union’s Falsified Medicines Directive (FMD). So important are these regulations that if a product soes not comply, it cannot be sold. Serialization is at the core of these regulations, to ensure the safety and integrity of all medicines produced and distributed, and to ensure accurate record-keeping to ensure their efficient recall and returns, if needed.
Challenges in Drug Recalls and Returns
Without serialization, the process of handling pharmaceutical drug returns and recalls is complex and fraught with challenges.
These difficulties can arise from regulatory requirements, operational inefficiencies, the specifics of the way the product is packed and the need to ensure patient safety while maintaining supply chain integrity.
Chief among the problems is the financial impact. Recalls and returns are expensive, involving product retrieval, destruction, and communication efforts. These high costs can strain resources and affect profitability.
Without serialization, there are also issues concerning a lack of visibility and traceability, making it almost impossible to trace drugs through the supply chain. Any resulting delays in identifying affected products can increase the scope of recalls and compromise patient safety.
Outdated systems can also cause issues if a product needs to be recalled, leading to errors and inefficiencies, with delays in processing returned drugs, or initiating recalls, increasing costs and risks.
There are also huge complexities in logistics that need to be addressed. Managing the return of drugs from pharmacies, hospitals, and distributors is logistically challenging, with improper handling resulting in delays, increased costs, and regulatory issues and patient safety
The challenges in pharmaceutical drug returns and recalls are significant but can be mitigated through serialization, automation, and robust data management systems. Proactive measures, clear communication, and regulatory compliance are essential to protect patients, maintain trust, and ensure supply chain integrity.
Indeed, modern serialization solutions increasingly enable the tracking of individual products right from the point of manufacture to being prescribed to a specific patient, a pattern which will become much more widespread as technology continues to develop.
Serialization’s Impact
Serialization has transformative effects on the pharmaceutical industry, particularly in streamlining the drug recall and return process. Furthermore, especially from the manufacturer’s point of view, it is also key to supply chain accuracy and inventory management.
The process has transformed the traceability of drugs by assigning a unique identifier to each drug package, enabling precise tracking of its journey through the supply chain. Therefore, if they need to be recalled, affected drugs can be quickly identified and traced back to their source, reducing the time and effort required to locate them.
It has also helped with targeted recalls by allowing manufacturers to pinpoint specific products or batches affected by an issue. Only the defective or compromised units are recalled, minimizing disruption, waste, and financial losses.
Serialization has also greatly improved efficiency. Data is stored in centralized systems that can be accessed in real-time which accelerates the recall process and inventory distribution by automating the identification, notification, and retrieval of affected products.
The automation of recalled products can also be helped. Serialization ensures that each product’s unique identifier can be verified against a database, meaning that counterfeit or diverted drugs can be identified and removed, ensuring only genuine products are returned to the supply chain.
Serialization also meets global regulatory requirements. This ensures that recalls and returns are conducted in compliance with legal frameworks, avoiding penalties and maintaining overall trust.
Case Studies
Recent years have seen several examples of drug recalls where serialization played a core role.
The key factor to bear in mind here is that no manufacturer is exempt from products being recalled. There are a host of issues that can go wrong – often outside the control of the manufacturer.
Robust serialization solutions can ensure the process is as swift and cost-effective as possible when it needs to happen, which – as the following examples show – ensures the manufacturer saves both money and is able to minimize the reputational damage caused.
One such occasion occurred during 2018 and 2019 when batches of medication used to treat high blood pressure and heart failure were found to contain dangerous impurities. Of course, this needed removing from the distribution cycle immediately. Manufacturers and distributors used serialized codes to identify and track the specific lots affected by the contamination, ensuring only the defective batches were removed from the market. (Valsartan Recall Expanded by FDA and European Medicines Agency | tctmd.com
Another example of note happened in 2017 when certain batches of EpiPen auto-injectors were recalled due to a defect that could prevent the device from delivering the correct dose of epinephrine. Here, serialization facilitated the identification of the defective devices by their lot numbers, ensuring precise removal and reducing the risk of unaffected devices being mistakenly pulled from shelves. FDA alerts consumers of nationwide voluntary recall of EpiPen and EpiPen Jr | FDA
In 2018 to 2020, medication used to treat the cardiovascular system needed to be recalled due to contamination. Unique identifiers on drug packaging allowed healthcare providers and patients to verify whether their medications were part of the recall, improving compliance and safety. Class 2 Medicines recall: Accord Healthcare Limited – Losartan Potassium 50mg Film-coated Tablets, PL 20075/0022 and Losartan Potassium 100mg Film-coated Tablets, PL 20075/0023 – GOV.UK
Future Trends
The future of pharmaceutical drug returns and recalls is being shaped by advancements in technology, evolving regulatory requirements, and increasing focus on patient safety and supply chain efficiency.
We will see a shift toward personalized therapies and smaller production runs. In one way, this will make things easier when it comes to traceability, but in another, it will make things more complicated. With more targeted recalls and returns, serialization systems will need to adapt to manage smaller, individualized batches which will require new and constantly evolving technology and solutions, requiring the expansion of serialization beyond current mandates, integrating more granular tracking at the unit level. Similarly, when it comes to personal medication, the speed of its recalls is also expected to significantly improve.
We will also see more reliance on artificial intelligence (AI) and machine learning (ML). The use of both to analyze supply chain data and predict potential recall triggers, such as manufacturing defects or adverse event patterns, will become much more frequent. Internet of Things (IoT) integration will also become more prevalent. IoT-enabled sensors and devices to monitor drug conditions such as temperature and humidity throughout the supply chain will become more common. This will enable early detection of issues, such as cold chain breaches, and automated recall or return triggers for compromised products.
A further trend is likely to centre around consumers becoming much more involved. Development of mobile apps and digital platforms allowing consumers to verify drug authenticity and report issues directly are likely to permeate throughout society, leading to the faster identification of counterfeit or defective drugs. Consumers will also be able to utilise their own wearable devices, such as smart watches and health monitors.
Conclusion
Serialization has, unsurprisingly, become vital for the pharma industry of today – and the future.
It is now entrenched across the production process, distribution and storage – and is all underlined by governments across the world making it a mandatory requirement.
While we have written at length about serialization’s role in fighting counterfeit drugs, and as an enabler for global regulatory standards, the fact that it is also core to swift, efficient recalls, also needs underlining.
There have been some concerning cases necessitating the recall of drugs. When it comes to the safety of patients, chances cannot be taken. The fact that serialization can aid the process, leading not only to increased consumer health, but also extra confidence in the pharma industry, cannot be overstated.